Online Stack Gas Analyzer
CEMS (Continues Emission Monitoring System)
A CEMS serves the single purpose of monitoring emissions for regulatory compliance and is not connected to any process control mechanism, although its data may be used to help evaluate combustion processes.
Here, we will focus on the types of installations frequently found in chemical plants and refineries: fired heaters, boilers and some heat-intensive processes. For the most part, these burn natural gas, oil or a combination of
plant byproducts. Each generates a list of pollutants connected with these fuels, primarily:
- nitrogen oxides (NOx);
- sulfur dioxide (SO2);
- carbon monoxide (CO);
- carbon dioxide (CO2);
- unburned hydrocarbons;
- ammonia (NH3 ), usually residue from a NOx suppression system; and
Other applications and fuels may result in a longer list of pollutants requiring monitoring but these tend to be more specialized.
y supplies systems that comply with local (IDOE), domestic and international regulations.
The number of measured components depends on the plant type, but also on the used fuel.
Our solutions:
-
Our solutions:
Common to all applications is the need to analyze the flue gas after it has received any treatment and as it is leaving the stack. Two main groups of analyzer techniques suit this task:
1.in-situ: where the analyzer is incorporated into the stack;
In-situ approaches represent a very small segment; so focuses on extractive methods, which differ in the type of analyzer technology and sample gas treatment. In particular, we concentrate on high-performing newer methods that are much simpler than older technologies and address operational and maintenance problems they pose.
2.extractive: where sample gas is drawn from the stack and sent to the analyzer.
2.1. Dilution extraction. This mixes untreated air with the flue gas to increase its volume and provide cooling. The underlying idea is that the higher volume supplies enough air to avoid condensation, even at a lower temperature. The additional air volume is measured and pollutant levels adjusted accordingly. How- ever, maintaining consistency is difficult because it requires very accurate measurement of sample and dilution air flows, and impurities in the dilution gas affect the readings. This approach mainly finds use for coal-fired applications where water vapor content is low.
2.2. Cold/dry CEMS. The most common extraction method for applications at chemical plants and refineries, it has been utilized for many years, so regulations frequently specify this approach or at least assume its use.
Cold/dry methodology passes the sample stream through a thermoelectric chiller to reduce the temperature to about 4°C (39°F), so most moisture condenses and drops out. This approach is mechanically complex but well-suited to an application such as a boiler fired with pipeline natural gas, where the primary pollutant is NOx. Unfortunately, it has problematic side effects, particularly with more-complex fuel situations and longer lists of monitored pollutants.
Some pollutants, particularly particulates and some acids, are water miscible and dissolve or get captured with the condensate and, thus, are effectively washed from the sample. This drastically reduces their concentration and makes the readings for those analytes ineffective. Therefore, in situations that require monitoring of water-miscible pollutants (NH3, HCl, HF), this approach is not suitable. Other analytes (NO2, SO2) are somewhat water miscible, so water removal can affect them; however, the error usually is quite small and regulatory bodies often are willing to accept a compensated reading from the dry gas sample.
2.3. Hot/wet CEMS. As analyzer technologies have evolved, some have become more tolerant of higher operating temperatures, making the need for chilled gas samples less important. This has helped launch a simple and effective sampling technique that is becoming more widely used: a hot/wet system.
Figure 2B shows a single sample stream flowing directly from the tap point to the analyzer without passing through a chiller. The sample stream is maintained as hot as necessary to keep all components above their dew point, so no condensation occurs. Where high concentrations of SO2 exist, the required temperature can be held at 160–190°C (320–375°F) to stay above the acid dew point.
All chemical components remain in their gas phase, just as they are in the flue-gas stream, during and after passing through the analyzer. When finished, the sample is vented, still as a gas, so there is no liquid at all in the system. The data processing system for the analyzer converts the wet readings to a dry basis as necessary (more on that point later). This approach is less complex mechanically than an equivalent cold/dry system, and calls for different analyzer technologies for some pollutants.
ANALYZER TYPES
Traditional cold/dry systems generally use a combination of established analyzer technologies suited to specific pollutants, including:
- non-dispersive infrared (NDIR) spectroscopy (CO, CH4, SO2, NO, NH3);
- non-dispersive ultraviolet (NDUV) spectroscopy (NO2, SO2);
- gas chromatographic (GC) analyzer (H2S, sulfur species);
- paramagnetic analyzer (O2); and
- chemiluminescent analyzer (NOx).
- Some of their capabilities overlap, so individual situations determine the selection of the specific In certain cases, the regulatory agency may drive the choice in one direction or another. For example, chemiluminescent analyzers long have served as the standard reference method (SRM) for NOx monitoring by the U.S. EPA (Method 7E Procedure) and are cited in standards, e.g., the European Standard EN 14792:2017, used by other regulatory agencies. The SRM is not necessarily the only permissible technology
- however, regulatory bodies will insist that any proposed alternative must perform as well as the Therefore, when considering a different technology to measure NOx, it is important to determine if it can cover the necessary range, particularly at the low end, and if the regulations require measurement of all NOx components separately or if they can be lumped together.
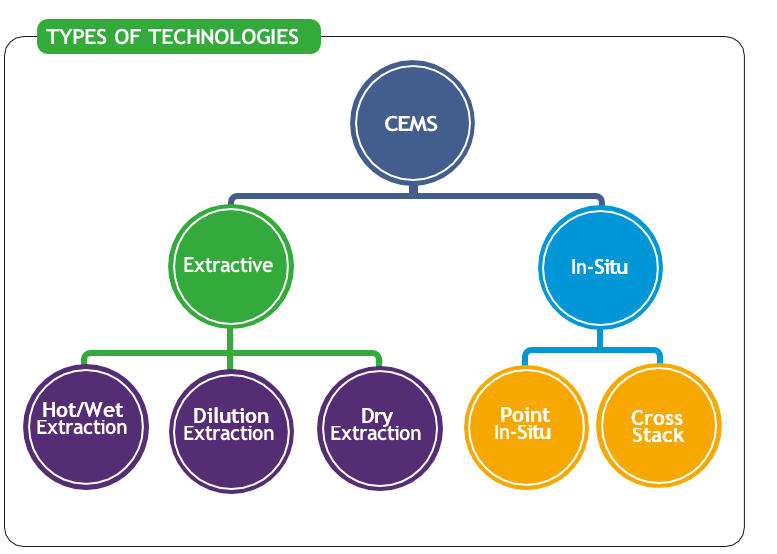
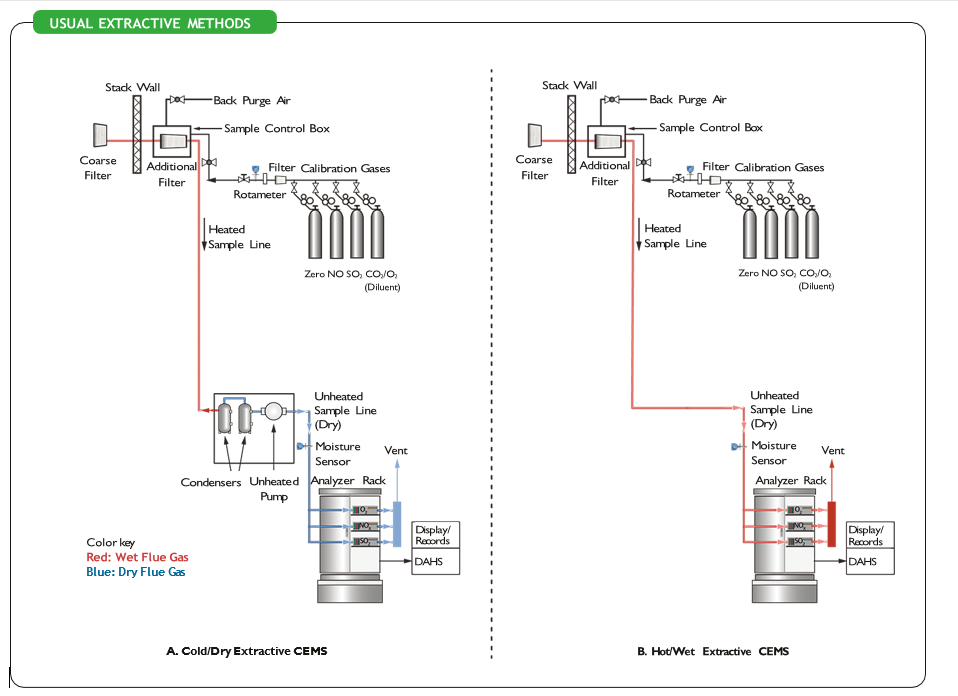